Design and manufacturing is often a collaborative effort that involves both internal and external teams. When communicating to vendors, it's easy to lose details in translation (sometimes quite literally). Whether you’re sourcing a quote or collaborating on product design, back-and-forth collaboration is always challenging. Email, snipping tool, and presentation decks are common practice for communicating needs, but this practice makes it challenging to stay organized.
Here are two types of documents you can create and maintain to stay organized in your back-and-forth: a Project Sketchbook and an Issues Tracker.
Project Sketchbook
A Project Sketchbook is a slide deck of every open to-do in the R&D phase. This is a great way to collaborate the status of parts and sub-assemblies and keep an internal history of the evolution of the product.
Here’s how to use it:
- Create a deck for your project (and share it with your coworkers, including mechanical engineers, electrical engineers, and manufacturing engineers). The deck will be divided into sections, each pertaining to a particular part or sub-assembly. Ideally this deck is cloud-based (Google Drive or SharePoint).
- Make a slide for every feature that needs to be changed and that you want to track. Here are some good things to include in the slide:
- The part / sub-assembly this issue falls under
- The owner of the issue
- Screenshots of CAD or pictures relevant to the issue
- Relevant diagrams, analyses, or sketches if not visible in CAD
- Link to the relevant CAD file(s) or PNs if you use a PDM
- The resolution of the issue (this is the most important!)
- Set the status of the issue:
- Open
- In Progress
- Monitor (hey, not all issues can be easily resolved and some need to be kept top of mind)
- Closed
- Review the Project Sketchbook weekly with the team to keep on top of issues
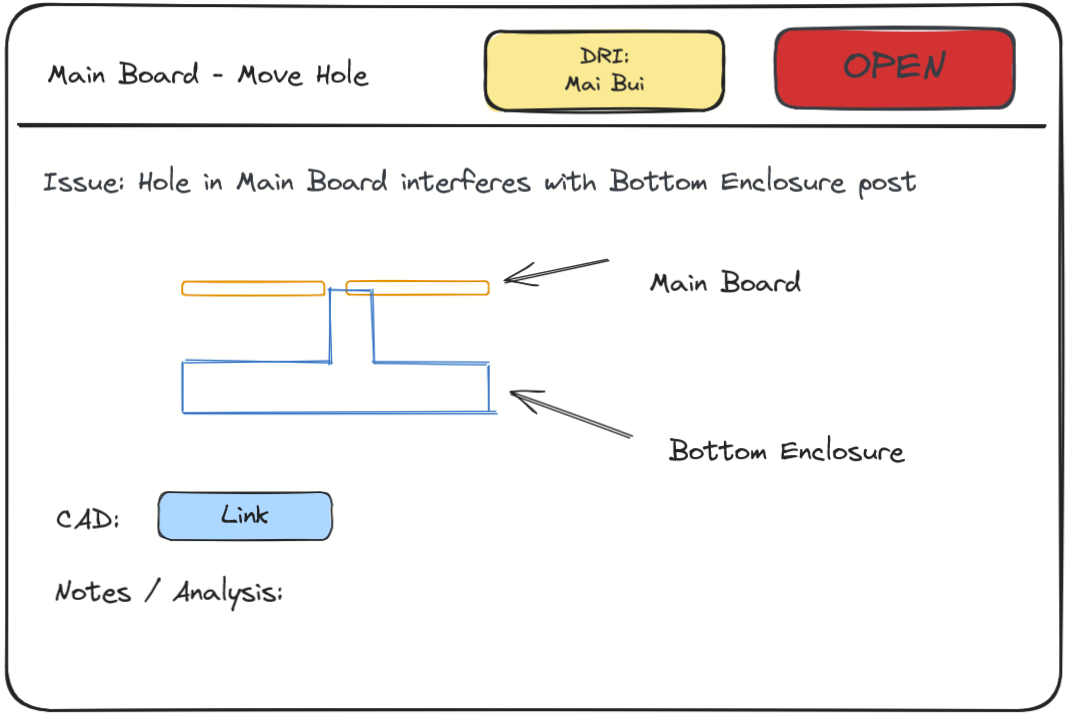
Issues Tracker
In conjunction with the Project Sketchbook, use an Issues Tracker to track open items in the pre-production and manufacturing phase. This is your tangible check-list to ensure that all issues related to manufacturing get resolved before entering into production (or resolve issues in production quickly).
Here’s how to use it:
- Create a deck for the project. It’s recommended to use the same deck throughout the entire NPI phase to make it easily searchable. As with the Project Sketchbook, ideally this is cloud-based.
- Add a slide for every issue identified. Be descriptive in naming the issue and include the date when the issue was first spotted. Numbering each issue is also helpful so you can easily refer to it.
- Set the status of the issue:
- Open
- In Progress
- Monitor
- Closed
- Make sure all stakeholders (including the manufacturing team) has access to the document so they can add and respond to comments.
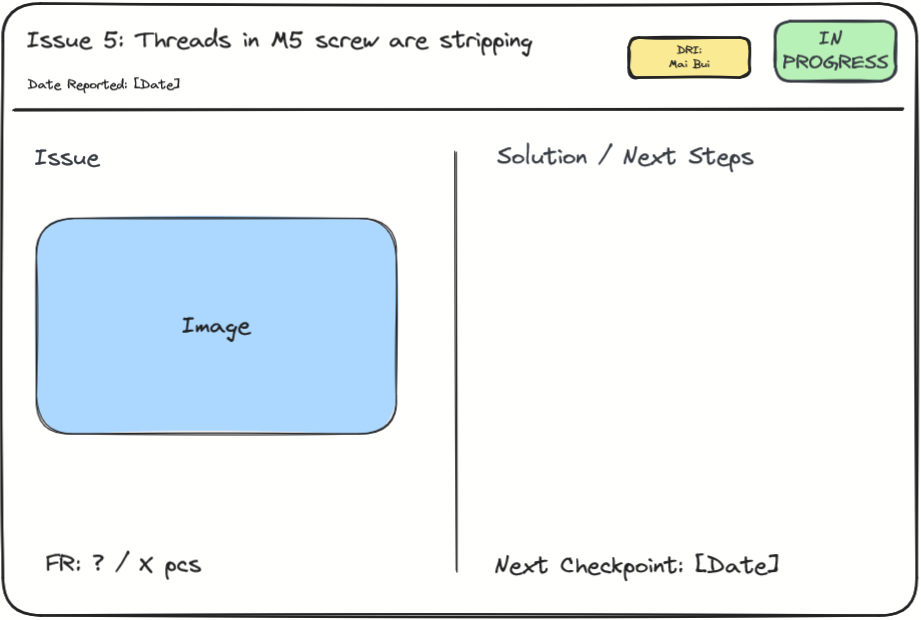
Special thanks to Liam Murphy, Senior Product Design Mechanical Engineer at Verkada, for sharing these templates and the magic behind them!
Stay tuned for new Quarter20 templates that will auto-generate this type of documentation for you and your teams.